Antriebstechnik
Strom vs. Diesel – Wohin steuern Baumaschinenantriebe?
von:Heinz-Herbert COHRS
GRUBE - Leise, kaum hörbar summend, belädt ein Radlader einen Muldenkipper. Voll beladen, setzt sich der Kipper ohne Motorengedröhn in Bewegung. Etwas entfernt arbeiten ein Raupenbagger und eine Planierraupe, ebenso leise. Das, was eine gespenstisch stille Baustelle der Zukunft sein könnte, entpuppt sich als eine Sandkiste, in der sich ein paar kleine batteriebetriebene Spielzeuge bewegen. Denn "echte" Baumaschinen ohne Dieselmotor wird es auf lange Sicht nicht geben ...
Elektrisch angetriebene Maschinen wie Mining- und Umschlagbagger oder Untertagelader werden auch zukünftig eine Ausnahme bleiben und höchstens Sandkisten vorbehalten sein. Aber warum, wo doch heute so viel von elektrischen Antrieben und Elektroautos gesprochen wird? Sollten die Baumaschinen der Zukunft nicht besser auch elektrisch statt von Dieselmotoren angetrieben werden?
Grundsätzlich schon, doch nur, sofern dabei "hinter die Steckdose" des Kabels oder der Akkuaufladung geblickt und der Strom umweltfreundlich erzeugt wird. Elektroantriebe für mobile Maschinen mit großem Leistungsbedarf stehen zudem vor einer Hürde, sollte die Forschung in nächster Zeit keine überraschenden Sprünge machen: Die Energiedichte von Akkupaketen ist nicht gerade rühmlich, demnach müssen große und sehr schwere Akkupakete mitgenommen werden. Das erhöht nicht nur das Leergewicht jeder Maschine, sondern verschlechtert die Energiebilanz und den Gesamtwirkungsgrad drastisch. Und hinterher geschleppte Kabel behindern und sind nicht praktikabel.
Die Energieerzeugung direkt "vor Ort" im Dieselmotor ist daher zumeist sinnvoller. Außerdem muss sich der Dieselmotor bei Energieverbrauch, Wirkungsgrad und Emissionen keineswegs verschämt hinter Elektroantrieben verstecken. Deutlich wird das bei den Wirkungsgraden: Ein Benzinmotor kommt auf nur etwa 32 %, ein Öl-, Kohle- oder Kernkraftwerk auf einen Wirkungsgrad von rund 35 %, aber ein einfacher Dieselmotor durch die Selbstzündung des Kraftstoffes bereits auf 39 %.
Hat der Dieselmotor einen Turbolader, werden es 41 %, kommt Ladeluftkühlung hinzu, steigert sich der Wirkungsgrad auf 44 %. Anders ausgedrückt: Fast die Hälfte des Kraftstoffes wird in Bewegungsenergie umgewandelt, während dies bei Kraftwerken nur etwa ein Drittel ist. Noch wird die Wirtschaftlichkeit des Dieselmotors durch keinen vergleichbaren Mobilantrieb übertroffen, auch nicht sein günstiges Verhältnis Gewicht/Dimension/Leistung.
Weil Konstrukteure ihre Köpfe rauchen ließen, sind die Abgase moderner Dieselmotoren so sauber wie noch nie. Mit den geltenden Grenzwerten Tier 4i/EU-Stufe IIIB wurde gegenüber den bisherigen Werten eine Reduzierung des Partikelausstoßes um 90 % und der Stickoxide um 50 % erzielt. Was in 16 Jahren seit der Einführung von Tier 1/EU-Stufe I erreicht wurde, ist daher enorm. Doch damit sind die Bemühungen keineswegs beendet: Mit den zukünftigen Grenzwerten Tier 4 final/EU-Stufe IV werden Partikelausstoß und Stickoxide auf nahezu Null reduziert. Anders ausgedrückt: Was vor weniger als zwei Jahrzehnten an Schadstoffen zu 100 % vorhanden war, wird bald annähernd verschwunden sein.
Fachleute bezweifeln jedoch, ob der technische Aufwand gerechtfertigt ist, die Abgase von Dieselmotoren fast schon grenzenlosen Säuberungsaktionen zu unterziehen. Um die Werte von Tier 4 final/EU-Stufe IV einhalten zu können, bleibt den Konstrukteuren nichts anderes übrig, als ihre Motoren mit "Abgas-Reinigungsfabriken" zu umgeben. Sowohl dem Einbauraum, der in vielen Maschinen eng ist, als auch dem vertretbaren technischen Aufwand sind hier Grenzen gesetzt.
Deshalb erscheinen andere Lösungen sinnvoller, die den Kraftbedarf der Maschinen reduzieren und damit auch Dieselverbrauch und Abgase. Doch solche Lösungen lassen sich nicht an jeder Ecke finden und sind für die Konstrukteure eine große Herausforderung.
Ein äußerst umweltfreundlicher Antrieb wurde nun bei einer Hubbühne vorgestellt: Der aus England stammende Pecolift für bis zu 3,5 m Arbeitshöhe wird motorlos angetrieben. So wirbt der Hersteller Power Towers auch mit den Worten "keine Akkus, kein Stromverbrauch, kein Hydrauliköl". Der 150 kg tragende Hubkorb wird durch ein patentiertes System bewegt, das 90 % des Hebegewichts zum Heben und Senken nutzt. Dazu erzeugt der Bediener mit einer Handkurbel schnell und bequem Bewegungsenergie, die in einem Gasdruckzylinder gespeichert wird. Dies sorgt für das Heben und Senken des Hubkorbes. Durch den Antrieb gehören Akkus, Kabel, Leckagen von Hydrauliköl und Abgase der Vergangenheit an.
Natürlich lässt sich ein Kurbelantrieb nicht für große Baumaschinen verwenden. Zukunftsträchtig sind hingegen Hybridantriebe, bei denen Schwenk- oder Bremsenergie zurückgewonnen und in den Antrieb eingespeist wird. Doch in der Praxis tauchen Hybridantriebe bei Baumaschinen nicht auf, abgesehen vom Raupenbagger HB215LC-1 von Komatsu, der inzwischen erfolgreich auf Baustellen eingesetzt wird.
Alle anderen Hybridbaumaschinen, die seit 2003 stolz auf Messen präsentiert wurden, gelangten nicht in die Serienproduktion. Das betrifft ein Dutzend Hybridmaschinen, meist Raupenbagger und Radlader, aber auch einen Mobilbagger und sogar eine Walze. Die oftmals angekündigten Termine für den Serienstart wurden in keinem Fall realisiert. Dies lässt vermuten, dass die meisten Hybridantriebe bisher vorwiegend als Marketing-Werkzeuge dienten.
Innovative, weil nicht elektrische, sondern hydraulische Hybridantriebe für Bagger werden nun auf der bauma von zwei Herstellern gezeigt, die für solide und praxistaugliche Technik bekannt sind. Mit dem 38-t-Raupenbagger 336E H stellt Caterpillar seinen ersten Hybridbagger vor, dessen hydraulisches Antriebssystem mit mehr als 300 Patenten geschützt ist. Gegenüber Baggern vergleichbarer Größe soll der Dieselverbrauch um rund 25 % geringer sein.
Der Bagger absolvierte bereits ausgiebige Testreihen, ist schon erhältlich und soll durch sein marktgängiges Konzept praxistaugliche, ausgereifte und bezahlbare Technologie bieten. Anders als bei bisherigen Hybridkonzepten verzichtet Cat auf einen Elektroantrieb und damit auf Hochspannungstechnik, Kondensatoren und Akkus. Im Bagger ist Hydraulik sowieso vorhanden, deshalb wird die Schwenkenergie in einem hydraulischen Druckspeicher aufgefangen und wieder an den Antrieb abgegeben. Zu den Vorteilen dieser Technologie zählen einfacher Aufbau, bekannte Komponenten sowie unkomplizierte Wartung und Reparaturen.
In anderen Größenordnungen rollt der neue Hybrid-Seilbagger HS 8300 HD an, den Liebherr auf der bauma vorstellt. Der 350 t wiegende Bagger eignet sich sowohl zum Schleppschaufel- als auch Greiferbetrieb, also für Gewinnung und Umschlag. Insofern durchschwenkt der Oberwagen stets große Winkel, weshalb sich die Rückgewinnung der Schwenkenergie ebenfalls lohnt.
Das Pactronic-System von Liebherr bewährt sich seit Jahren bei der Energierückgewinnung in Hafen-Umschlagmaschinen. Durch das Speichern und anschließende Nutzen überschüssiger Energie wird zum einen die Förder- und Umschlagleistung erhöht, zum anderen der Dieselverbrauch verringert. Die Technologie mit dem hydraulischen Energiespeicher sorgt für geringen Wartungsaufwand und hohe Zuverlässigkeit.
Baumaschinen weisen im Vergleich zu Pkw, Lkw, Bussen und anderen Maschinen extrem unterschiedliche Arbeitsweisen und damit auch Bewegungsabläufe auf. Weder bei Planierraupe noch Rammgerät lassen sich nennenswerte Energiemengen beim Bremsen zurückgewinnen. Deshalb begeben sich die Konstrukteure nun auf die Suche nach Antriebslösungen, die sich zwangsläufig von Maschine zu Maschine unterscheiden. So wählte Caterpillar für die 26-t-Planierraupe D7E erstmals einen dieselelektrischen Antriebsstrang. Der verbraucht bis zu 30 % weniger Kraftstoff als ein Antrieb mit Drehmomentwandler. Andererseits stellte Cat im vergangenen Jahr den weltweit ersten Radlader mit einem Leistungsverzweigungsgetriebe vor. Bei dem 24-t-Lader 966K XE werden die 220 kW (299 PS) Motorleistung je nach Bedarf und Arbeitssituation in einen hydrostatischen und einen hydromechanischen Antriebspfad verzweigt.
Normalerweise werden kleinere Radlader hydrostatisch, größere dagegen über Drehmomentwandler angetrieben. Beim 966K XE wurden nun die Vorteile beider Antriebsarten in einem stufenlosen Variatorgetriebe vereint, durch das der Motor stets in einem effizienteren Betriebsbereich arbeitet. Dieses CVT-Getriebe (Continuosly Variable Transmission = kontiniuerlich variables Getriebe) bringt Verbesserungen der Kraftstoffnutzung von bis zu 25 % pro Tonne geförderten Materials.
Gänzlich anders ist der Antrieb, den Sandvik für den Hybrid-Zweiwalzenbrecher CR810 konzipierte: Dort stört kein höheres Gewicht. Deshalb entwickelten die Ingenieure einen Schwungradantrieb. Kurzzeitige Leistungsspitzen werden mit zwei mächtigen Schwungrädern an beiden Seiten der Brecherwellen kompensiert, die von je einem 1250 kW starken E-Motor durch Riemen angetrieben werden. Die Schwungräder speichern mit ihrer großen Eigenmasse viel kinetische Energie, die bei schwer drehenden Brecherwellen sofort abgegeben wird und so den Antrieb wirksam unterstützt.
Einsparungen von bis zu einem Viertel des Kraftstoffverbrauches sind mit zwei statt einem Motor möglich, wie Wirtgen bei den großen Kaltfräsen W 210 und W 250 unter Beweis stellt. Bei vielen Betriebsarten wie Transportfahrten, Umsetzen auf der Baustelle, leichtem Oberflächenfräsen oder bei Wartezeiten genügt für den Antrieb nur ein Motor. Erst bei höheren Leistungsanforderungen wird der zweite Motor automatisch zugeschaltet und digital mit dem ersten synchronisiert.
Bei der 76 t wiegenden Umschlagmaschine LH 80 M Litronic nutzt Liebherr das mit einem Innovationspreis ausgezeichnete Energierückgewinnungssystem ERC, das die Energie beim Absenken der Ausrüstung speichert und beim Anheben wieder freigibt. Dazu wird Gas in einem zusätzlichen, dritten Auslegerzylinder komprimiert. Beim Anheben unterstützt die im Gaszylinder gespeicherte Energie die beiden Hubzylinder, was zu höheren Umschlagleistungen und deutlichen Dieseleinsparungen führt.
Eine andere, bei Hafenkranen bekannte Technik sorgt beim neuen Umschlaggerät 8130 EQ von Sennebogen für Einsparungen, denn durch ein bewegliches Gegengewicht entfällt der Kraftaufwand für das Heben des Auslegers nahezu gänzlich. Selbst bei großen Lasten und Reichweiten muss nur das Lastgewicht bewegt und angetrieben werden, was einer enormen Kraft- und Energieersparnis gleichkommt und die Energiekosten um bis zu 50 % senkt. Gemeinsam mit dem elektrohydraulischen Antriebskonzept werden weitere große Einsparungen erzielt.
Die Möglichkeiten, den Energiebedarf zu mindern und damit Kraftstoffverbrauch und Abgasemissionen zu reduzieren, sind sehr vielfältig, hängen aber in starkem Maße von der Art und Arbeitsweise der betreffenden Maschinen ab. Deshalb wird es einen allgemein anwendbaren Hybrid- oder Energiesparantrieb für Baumaschinen in absehbarer Zeit nicht geben.
ABZ-Stellenmarkt
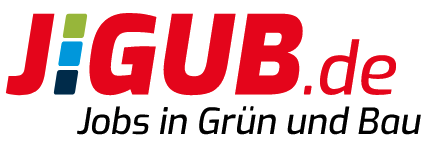
- Themen Newsletter Baumaschinen bestellen