KDI-Motoren
Montagelinie zeichnet sich durch hohe Automatisierung aus
REGGIO EMILIA/ITALIEN (ABZ). - Das Werk von Lombardini in Reggio Emilia wurde als Kompetenzzentrum der Kohler-Gruppe ausgezeichnet. Am Produktionsstandort in Reggio Emilia werden die neuen KDI-Motoren hergestellt, welche die Normen Tier 4 Final – Stage IIIB erfüllen. Das Streben nach Spitzenleistung in der Produktqualität, beim Kundenservice und bei der Wettbewerbsfähigkeit war auch bei der Auswahl der Produktionsprozesse die treibende Kraft. Die Widersprüche zwischen einigen dieser "treibenden Kräfte" wurden dank der verwendeten Produktionsstrategie in Einklang gebracht. Die Nähe zu den beiden Hauptseehäfen Italiens am Mittelmeer (Genua und La Spezia) gewährleistet einen schnellen Materialfluss, wodurch die Nachfrage von Kunden in Europa und der ganzen Welt erfüllt werden kann. Des Weiteren gewährleistet die Anwesenheit des technischen Managements, die während der "Start-up"-Phase eines hochtechnologischen Produkts, wie es die KDI-Motoren sind, erforderliche unmittelbare und angemessene Unterstützung. Die Montagelinie des KDI zeichnet sich durch ihre hohe Automatisierung und dem ausdauerndem Streben nach Spitzenleistung aus. Das Konzept der Objektivierung des Produktionsprozesses wurde mit dem Ziel, den Endabnahmeprozess auf dem Prüfstand auf ein Minimum zu reduzieren, auf die Spitze getrieben. Für die Endabnahme wird ein gemischter Prozess von "heißen" Prüfungen mit laufendem Motor und "kalten" Prüfungen mit geschlepptem Motor angewandt. Insbesondere sind Warmprüfungen für Motoren mit mechanischer Einspritzanlage notwendig, während wir für Common-Rail-Motoren eine Kaltprüfung wählen. Das Ganze in Übereinstimmung mit den neusten und fortschrittlichsten Technologien, die heute in der Welt der Dieselmotoren für Industrie und Automobilbranche zum Einsatz kommen.
Die momentan installierte Produktionskapazität beträgt 33.000 Motoren/Jahr in zwei Schichten, leicht verdoppelbar mit einer "Vorlaufzei" von acht bis zehn Monaten.
Hinsichtlich der mechanischen Endbearbeitung der Kurbelgehäuse haben wir Möglichkeit von zwei (für 26.000 Stück/Jahr) auf fünf (für 65.000 Stück/Jahr) Arbeitszentren für die Verarbeitung von Grauguss der neuesten Generation staffelbare Lösung vorgesehen.
Die Arbeitszentren sind in eine automatisierte Zelle eingesetzt, die gleichzeitig jeden Motorgehäusetyp von 3- bis 4-Zylindern bearbeiten kann. Die gleiche Zelle versorgt die Zylinderschleifmaschine, den Hochdruckreiniger mit positionierten Strahlen und die Dichtheitsprüfmaschine. Das Alles zur Gewährleistung höchster Präzision und Sauberkeit vor der Montagephase.
Dies ist das deutlichste Beispiel für eine Produktionslösung, die den besten Kompromiss zwischen preislicher Wettbewerbsfähigkeit und hohen Qualitätsstandards erreichen kann. Denn während Gussteile und Halbzeuge aus Schwellenländern importiert werden, erfolgt die Hightech-Endbearbeitung intern mit speziellen Prozessen. Alles eng verbunden mit der Montagelinie.
ABZ-Stellenmarkt
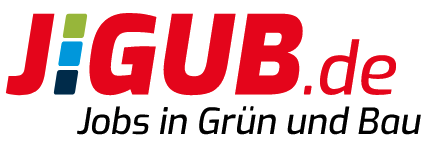